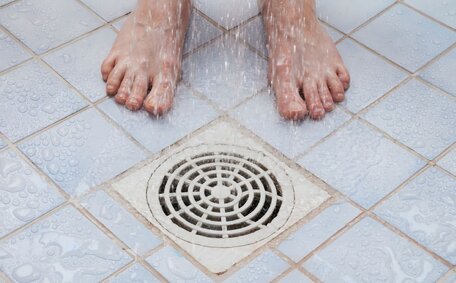
Baking Soda & Vinegar for Cleaning
Using baking soda & vinegar separately for cleaning is very effective; but mixing them dilutes their cleaning power. Learn how to use them properly.
Read MoreUnder typical conditions for pipe relining, epoxy resin can last between 50 to 100 years. Epoxy resin achieves its full lifespan under the following conditions:
The moderate coastal climate of Lilyfield, Sydney, is ideal for the longevity of epoxy resin. Moreover, formula advancements over time have enhanced the product’s durability. Modern epoxy resins used in pipe relining are resistant to chemical corrosion, humidity, mechanical wear and other potential causes of degradation.
Industry safety standards such as NSF/ANSI 61 guarantee that modern epoxy resins are safe, effectively protecting potable water systems from contamination. Designed for durability, epoxy resin pipe relining provides a long-term solution, reducing concerns about its lifespan.
With appropriate care and maintenance, epoxy resin liners can reach their full potential lifespan of 50 to 100 years. This necessitates prompt inspection of any issues by a certified plumbing professional. We recommend scheduling a biennial routine inspection of your pipe system to preempt and thwart potential problems.
Ultimately, epoxy resin outperforms traditional piping, proving to be a superior option for long-term pipe restoration. Relining with epoxy resin is more economical, faster, and less disruptive compared to the comprehensive overhaul required for traditional pipe replacement.
Proper storage and handling before installation are essential to maximise the durability of epoxy resin. This care ensures the epoxy resin product can retain its effectiveness throughout its substantial 50-100 year service life.
Store unmixed epoxy resin in tightly sealed containers at temperatures between 15 to 30°C, avoiding direct sunlight and moisture. The hardener component can absorb water, which compromises its shelf life. Keeping resin in a cool, dry storeroom prevents problems like premature curing or viscosity issues.
Contamination from dirt, grease, oil or other chemicals can inhibit curing. Therefore, it’s essential to store unused resin in its original, airtight packaging. Use any opened containers quickly for your relining projects, or discard them if they harden.
To activate resin for pipe relining, strictly follow the manufacturer’s guidelines for combining the resin and resin hardener components. Using calibrated metering pumps ensures you achieve the right 1:1 ratio between components. An improper mix can dramatically affect the resin’s performance and service life.
Also, mix only as much resin as necessary for each relining job. Dividing batches into smaller quantities reduces wastage and ensures you apply freshly catalysed product at its optimal pot life. Should the resin harden too soon in supply lines or injection equipment, its effectiveness could be compromised.
Ultimately, proper storage keeps epoxy viable over time, while precise handling and mixing activates it for maximum durability. Following guidelines ensures the longevity of the epoxy, supporting its expected 50 to 100-year lifespan.
When selecting an epoxy resin product for pipe relining, it’s important to verify that it meets key safety and performance standards. Various certifications back up claims about durability and service life estimates.
Epoxy resin for residential potable water system relining must comply with NSF International’s NSF/ANSI Standard 61 for health and safety. This rigorous toxicology review ensures formulations contain nothing that could leach chemicals into drinking water at levels deemed hazardous.
NSF certification affirms that the epoxy resins are safe for use in potable water systems. Thus, products carrying this certification reassure users of their 50 to 100-year service life claims without the risk of contamination.
Reputable epoxy resin makers also backup longevity estimates by testing chemical resistance. ASTM testing standards like ASTM C581 evaluate resin’s immunity to issues like environmental stress cracking when exposed to common household chemicals.
Products that pass these tests prove their durability when in contact with chemicals. This suggests an enhanced service life even for household drainage systems subject to cleaning products, oils, solvents and other potentially damaging substances via sinks or drains.
Further, material hardness tests like ASTM D2240 confirm resilience, reinforcing the claimed 50 to 100-year service life.
Adherence to the widely recognised ISO 9001 quality management standard also indicates the credibility of epoxy resin products. This certification requires consistency in meeting durability, longevity and food-safe standards over time.
Epoxy resin producers adhering to ISO standards demonstrate a solid commitment to their 50 to 100-year lifespan guarantees. ISO compliance reflects a dedication to best practices, corroborating these lifespan claims.
Ultimately, respected safety certifications underscore epoxy resin’s reputation for outstanding longevity, distinguishing it from conventional pipe solutions. Pipe relining customers can have faith in this innovative solution’s extended service life.
Recent advancements in epoxy resin technology for pipe relining have produced more robust formulations with improved longevity.
Cutting-edge epoxy blends flaunt exceptional broad-spectrum chemical resistance compared to their predecessors. Contemporary testing more accurately reflects real-life chemical exposure from substances like cleaning agents, oils, and wastewater.
Its heightened resistance to acids, alkalis, solvents, and other reactive substances forestalls premature degradation, reinforcing its 50 to 100-year service life.
The continuous quest for improved temperature/pressure ratings sees contemporary resin grades handle hotter fluids or mechanical stresses that would previously impact pipe integrity.
Improving Shore hardness, adhesion, flexural modulus, and heat deflection enhances the material’s resistance to physical wear. This better withstands physical rigours inside pipe systems.
Multi-layer lining configurations are now better tailored to meet the needs of demanding applications. Using layers like fibreglass between resin coats accommodates greater pipe ovality or rotational shear.
Smart layering prevents pinholes at joints/branches and minimises strain. This caters to awkward pipe routes facing movement, optimising durability.
Automated spinning sprayheads deliver a smoother and more uniform resin application than manual hand-rolling techniques. This gives fewer defects and improved corrosion protection.
Better impregnation in damaged areas and 360° contact integration with the existing pipe also enhance longevity. Overall, technological progress translates to notable on-site application gains.
At Lilyfield Plumbing, we embrace the latest epoxy solutions to offer our clients unrivalled durability and confidence in long-term pipe repair.
Using baking soda & vinegar separately for cleaning is very effective; but mixing them dilutes their cleaning power. Learn how to use them properly.
Read MoreBlocked drains are usually caused by buildup of hair, grease, debris and more in your pipes. Fix the problem with professional drain unblocking services to get your drains flowing freely again. Contact us for affordable drain unblocking.
Read MoreWhen you suspect a gas leak or damaged gas line, contact a licensed gas fitter immediately to locate and repair it. A gas line repair involves sealing leaks, replacing corroded or damaged pipes and testing all connections for safety before restoring gas supply.
Read MoreLilyfield, 2040 NSW
We will call back as soon as possible.